INJECTION RUBBER MOLDING MACHINE
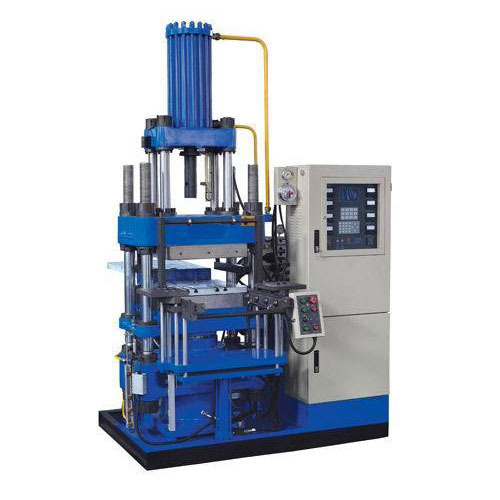
Adopting high precision pressure sensor, servo motor, high precision encoder, during operation, the pressure and flow are real time comparison, control error is controlled by specific PID controller.
- SWIFT DYNAMIC RESPONSE
High performance pump and synchro servo motor, fast response, short deceleration distance, high speed and stability.
- INSTANT POWER CONSUMPTION MANAGEMENT
Equipped with electronic wattmeter, instant power consumption data will be processed by B&R S98 controller for machine performance and production analysis.
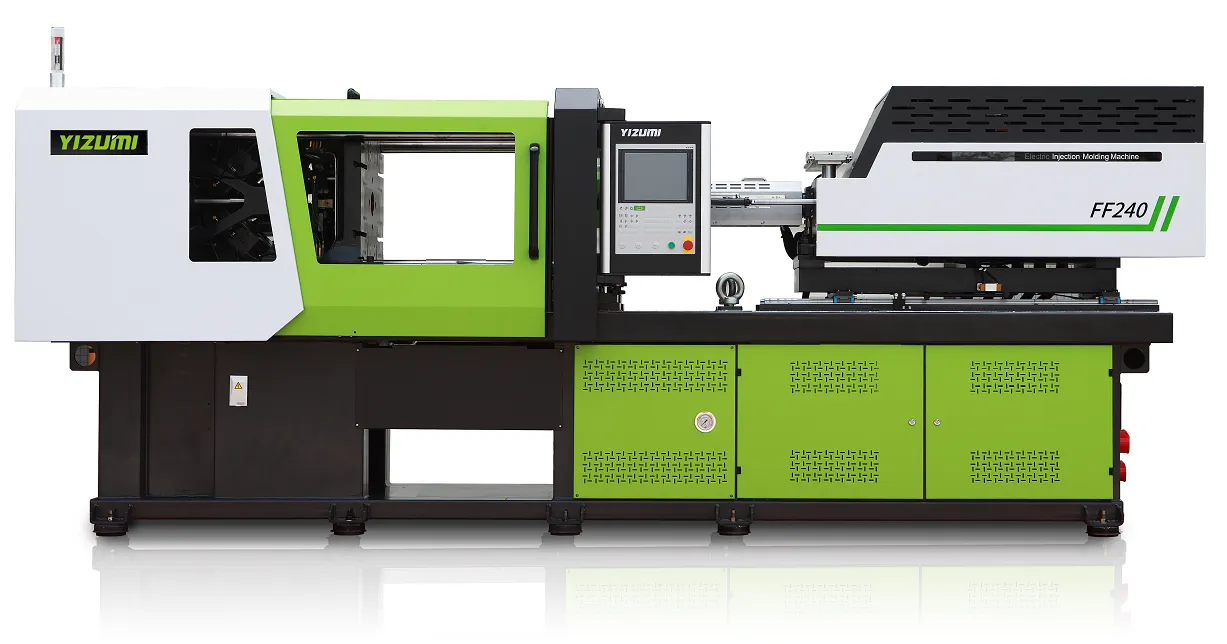
PREVENTIVE MAINTENANCE
HYDRAULIC OIL:
Easy oil shortage will cause the oil temperature increases, the air is easy integration into the oil and hydraulic oil to affect the normal operation of the system, fuel oil, or less than is usually due to loss of repair, this routine should be aware that there is no leak check site, early replacement of worn seals, tighten loose joints, repaired fuelto check in time supplies.
FILTER CLEANING:
Oil filter plays the role of clean hydraulic oil, the oil filter should be cleaned once every three months to maintain the smooth flow of the oil suction tube Ga, also check the oil filter network for damage.
COOLER CLEANING
Cooler should be cleaned once a year, or according to their ability to work has reduced the cleaning, cooler internal blockage or fouling will affect both the cooling efficiency, cooling water should choose soft (no minerals) is better
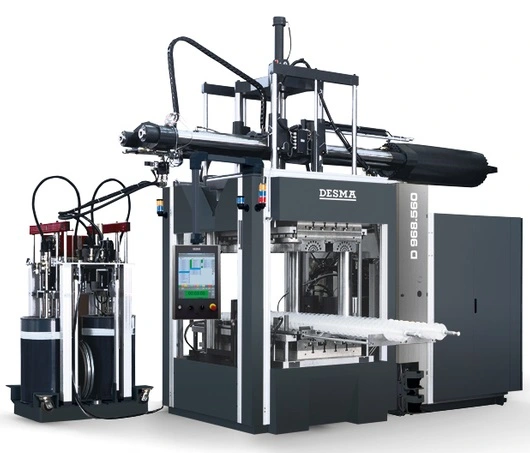
BREAKDOWN
The whole injection moulding process usual lasts from 2 seconds to 2 minutes. There are four stages in the cycle. These stages are the clamping, injection, cooling and ejection stages.
MACHINE INSTALLATION
The analysis of floor bearing capacity should be carried out by civil engineering experts.
If the injection machine is installed on reinforced concrete floor, generally any preparations for the foundation are unnecessary.
If the machine is installed on ordinary workshop floor, corresponding foundation should be prepared.
Max. Surface pressure applied by the machine onto the concrete floor may be calculated according to the machine weight as well as the number and area of adjustable shims.
Middle and large machines should be fixed on the foundation with foundation bolts.
Adjustable shims are supplied with the machine. Please refer to Section 2.8 for use of adjustable shims. Please note that adjustable shims reduce the contact area of floor and thus increase the pressure applied by the machine on the floor. Ensure the floor bearing capacity can bear this pressure.